

The proposed pulse feed mode and transient model is a new approach that can provide a theoretical basis for improving the MD performance, optimizing the operating parameters, and filling the gap in the numerical simulation of MD. Using the optimal pulse parameters, the effects of the pulse feed were more pronounced with a shorter membrane module length and when the feed temperature, velocity, and concentration were higher. The simulation results demonstrate that the pulse feed mode could guarantee the operation of the VMD system at a high thermal efficiency and significantly improve the MD flux.
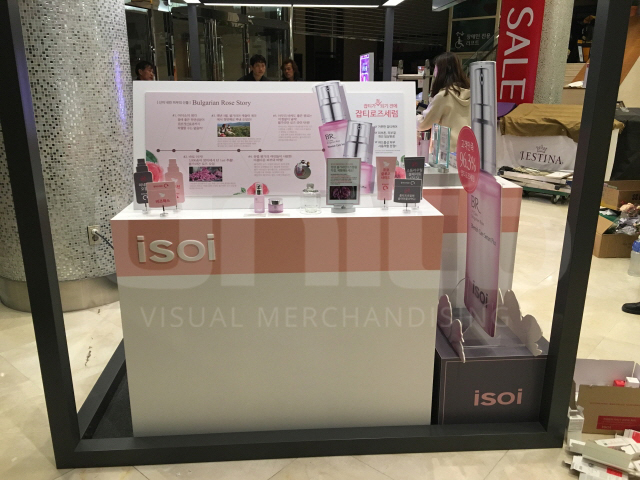
Therefore, a two-dimensional computational fluid dynamics (CFD) transient VMD model was established herein. Conventional steady-state simulations cannot fully and clearly demonstrate the dynamic changes in the VMD performance parameters over time during the pulse feed. To increase the disturbance of the feed near the membrane wall, reduce the adverse effects caused by the temperature polarization, and improve the membrane flux, an innovative vacuum membrane distillation (VMD) operation mode was proposed, in which the traditional steady-state feed is replaced with the pulse feed. Temperature polarization has a significant impact on the efficiency of membrane distillation (MD) systems and leads to a decrease in the overall thermal efficiency and MD flux. Additionally, CFD predictions confirmed that there was a reasonable conformity between the predicted values of the model and the experimental data. Moreover, considering the coalescence and break-up impressed the results significantly. The simulation results revealed that the presence of a draft tube in an air-lift reactor causes to significant enhancing the gas-liquid mass transfer rate, and reducing the average liquid velocity and the average gas holdup. Additionally, the effect of draft-tube was considered in simultaneous with the coalescence and breakup for evaluating the reactor performance. Moreover, the intricate mathematical model was employed for investigating the coalescence and breakup towards a more precise simulation of the air-lift reactors. This work is mainly aimed to present an insight into the effect of draft tube on the air-water reactor mass transfer and hydrodynamics.

Two dimensional computational fluid dynamics (CFD) simulations of internal air-lift reactors were considered to predict hydrodynamic and mass transfer in the unsteady state flow. With the novel pyramidal distributor, a maximum permeate flux of about 72 kg/m2h was achieved at feed inlet temperature of 358.15 K, vacuum level of 87 kPa, and feed interstitial velocity of 0.085 m/s. The optimized distributors significantly enhanced the VMD permeate flux of the CF-MM. Compared with the permeate flux of CF-MM without a distributor, the permeate flux increased to about 5% of the flat-plate distributors, and to about 6% to 12% of the pyramidal distributors. Two kinds of liquid distributors in flat-plate and pyramidal forms were fabricated and used to study their performances in VMD. The pyramidal and dome-like distributors have better liquid distribution than the flat-plate distributor. Based on the simulation results, the structural parameters of the liquid distributors were optimized to achieve an even liquid distribution. The feed flow conditions were simulated and calculated. Based on the characteristics of the CF-MM, a three-dimensional liquid flow model was built in the shell side of the CF-MM.

To enhance the vacuum membrane distillation (VMD) permeate flux of cross-flow membrane module (CF-MM), three kinds of novel liquid distributors were designed and evaluated by computational fluid dynamics (CFD) simulation.
